2024-10-21
Efficiency Work at Spaljisten
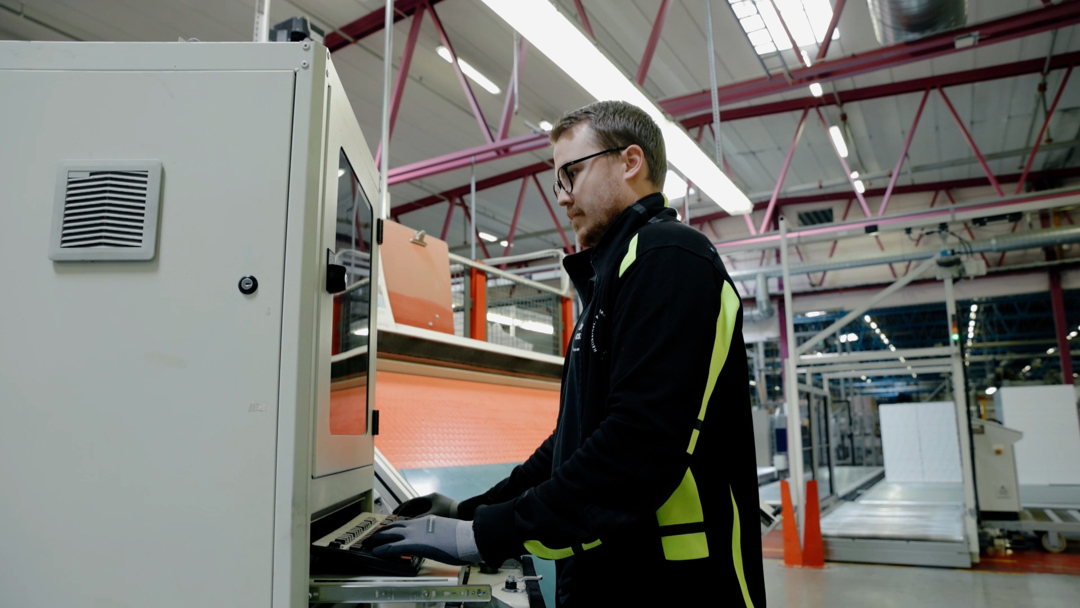
Jonatan Fransson
Interview with Jonatan Fransson, Production Supervisor for Processing
At Spaljisten, a comprehensive efficiency work is in progress, focusing on creating a standardized workflow throughout the entire production. The goal is to ensure quality and safety while achieving increased flexibility. There is also an aspiration to streamline the onboarding process for new employees and establish clearer routines for all staff members. Jonatan Fransson, Production Supervisor for Processing, shares his insights on the work.
A Dynamic Policy for More Efficient Production
The commitment is long-term, with the goal that all operators, both new and experienced, will follow the completed instructions in order to achieve consistent level of quality. At the same time, the new routines must be flexible enough to adapt as production evolves.
Currently, the efficiency work is in its early stages. However, Jonatan’s two processing lines, IMA and Homag 7, have made the most progress, with IMA serving as a pilot project that sets an example for other workgroups.
Together with technicians and machine operators, the work group has identified critical aspects for ensuring quality and safety. A competence matrix and a checklist have been compiled to standardize work processes and create a consistent approach throughout the production. The work also involves reviewing standard instructions that everyone must follow, testing them, gathering feedback, implementing, and starting to work according to these guidelines. Moving forward, the aspiration is to see results through more flexible production.
Transparency and Communication
One of the biggest challenges in the efficiency work has been getting everyone to understand why the changes are being implemented. Jonatan emphasizes the importance of clear communication:
"Being in agreement about why we are doing this is something that will make the work much easier."
He tells of an exercise where employees were asked to draw a pig without any directions, which led to vastly different results. Later, when everyone was given clear instructions, the results turned out much more uniform — a concrete example that helped many understand the difference in outcomes when following shared guidelines.
A Structured Approach
The efficiency work is closely linked to how employees' skills are assessed and how salaries are determined. Using a competence matrix makes it clear to each employee what is expected at different levels of their role.
"It makes it easier to hold employee discussions and assess which skills an employee has or can develop further," says Jonatan.
The efficiency work is being carried out in close collaboration between different workgroups in the production. Progress and challenges are a recurring discussion topic in weekly meetings. There should be no difference in how the work is carried out in different group. Setting a standard is crucial already at this stage.
A Positive Outlook on the Future
Jonatan is pleased with how the work has progressed so far, especially regarding the implementation of the onboarding process. Establishing a standard for training new machine operators has been a significant step forward. Together with the machine group supervisor, they have established a good standard. It’s easy to follow for those learning the job, those responsible for the training, and for a leader to follow up.
Looking ahead, Jonatan sees the biggest challenge in ensuring compliance in practice. Many machine operators have been with the company for a long time and have their own set ways of working, which requires an understanding of why standardization is important. But with continued follow-up and communication, he remains optimistic about the future:
"It feels like we are on the right path, even though there is still a long way to go."