Quality assurance
Our quality assurance work involves:
• Reducing KPIs related to cost of poor quality.
• Incident management and root cause analysis.
• Internal and external auditing.
• Systematic measures together with sub-suppliers and customers.
• Dedicated change teams and steering group meetings.
• Risk analysis and process development.
• LEAN production – working smarter with daily tasks.
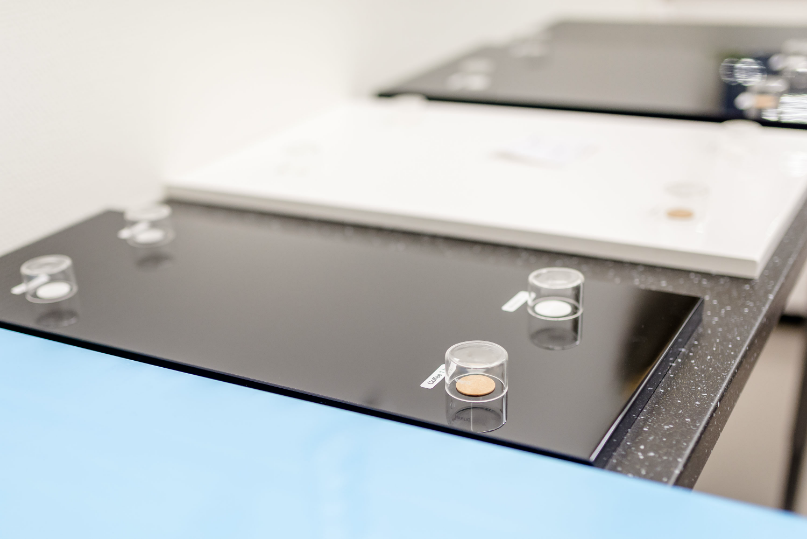
LAB operations
Spaljisten has an internal quality assurance lab in place in the production in Åseda. This helps to ensure that all quality requirements are complied with and that we meet our customers' expectations. Product quality is checked continuously through tests with steam, water and heat in several steps, and we also perform tests for stain resistance on a number of products. We want to ensure following regulations and laws and comply with customer agreements. Thus, external tests are also performed to ensure compliance.
We stand by our promised quality!
In addition to those mentioned above, visual control is a vital aspect of this work. These are documented and initiate QA processes that quickly lead to corrective measures and improvement activities to adjust production. In the case of any deviations, we handle all defects according to a set non-conformity process.
- Not a single product leaves our factory flow without rigorous testing. We never compromise on quality.
CARL-MAGNUS LUNDIN, QUALITY CONTROLLER
Certifications
We are a company who are eager to look after our employees, and the laws and regulations in the industry to make sure we deliver the best service and world-class products in the furniture market. We are proud to meet the requirements for IWAY, IWAY Forestry and GO/NOGO. We have the following certifications.
Spaljisten is FSC® certified (Forest Stewardship Council®)
(FSC-C114672)
NEWS
Ready to try us out?
We have a concept line installed which enables us to produce fronts for testing - with quick delivery. Perfect for you who wishes to try out the possibilities with us!